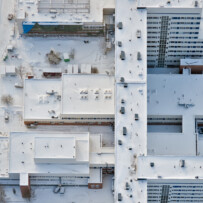
It may seem like last winter ended not too long ago, but the reality is that fall is quickly coming to an end, and colder temperatures and harsh weather are not far off. As a building owner or facility manager, planning for winter’s ice and snow starts at the top: The roofing membrane serves as the first line of defense against the elements. For roofing professionals, this is an opportunity to be a proactive partner with customers.
While internal staff may be tasked with performing basic roof inspections throughout the year, it is always a good precaution to hire a roofing professional for a detailed inspection before the weather turns. This can prevent minor roofing issues from becoming major concerns.
A close-up inspection of the roof can keep today’s small punctures, damaged flashings or torn seams from turning into tomorrow’s growing leaks, rising energy bills or spreading mold. Professional roofing contractors are intimately familiar with system specifications, installation, and how a finished system should look and perform.
GenFlex Roofing Systems has a reputation for durability over three decades and more than a billion square feet of installed membrane, so we know what to look for on a low-slope commercial system:
- Start with the basics:Clear debris and then inspect those areas for any damage. Also, take note of standing water (a low-slope roofing system is designed to drain within 48-72 hours after rain). If areas of the roof are sagging, another harsh winter may compromise the integrity of the roofing membrane.
- Don’t forget the seams: A roofing expert will be able to better inspect the seams between membrane sheets. Even though roofing systems are designed to withstand the elements of winter, problems are more likely to form around the seams.
- Check for “thermal shock”: This problem is a leading cause of roof failure. As the seasons change, thermal conditions cause roofing materials to expand and contract. So when the stress of the expansion and contraction exceeds the strength of the material, you can find cracks or splits forming. GenFlex roofing membranes are designed to maintain elasticity, flexing to resist the thermal cycles that come with the extreme changes in weather. But as the roofing membrane ages, the materials become less flexible and more prone to splits in the membrane.
- An electric capacitance meter provides an easy, affordable leak-detection tool – it transmits low-frequency signals through the membrane that identify elevated moisture levels.
- Infrared cameras can also provide contractors with a color-coded ‘map’ of moisture under the roof surface, with a graphic display of temperature variations.
GenFlex stands behind its systems
GenFlex Roofing Systems utilizes its network of authorized contractors to repair or replace roofing if necessary, connecting with building owners within a day according to the system warranty. GenFlex contractors can play a valuable role in streamlining this process, while also being qualified to inspect other systems that may be more susceptible to wear and damage.
In short, a comprehensive roof inspection for a commercial facility is much more than a quick scan and a checked box – especially when winter storms lurk right around the corner. Done properly, pre-winter inspection and repairs demand the skills of a roofing professional – a value-added opportunity for the proactive contractor.
If you find a leak or tear in your roof, contact GenFlex right away. We will connect you with a quality, local roofing professional immediately. Click here to start the process.